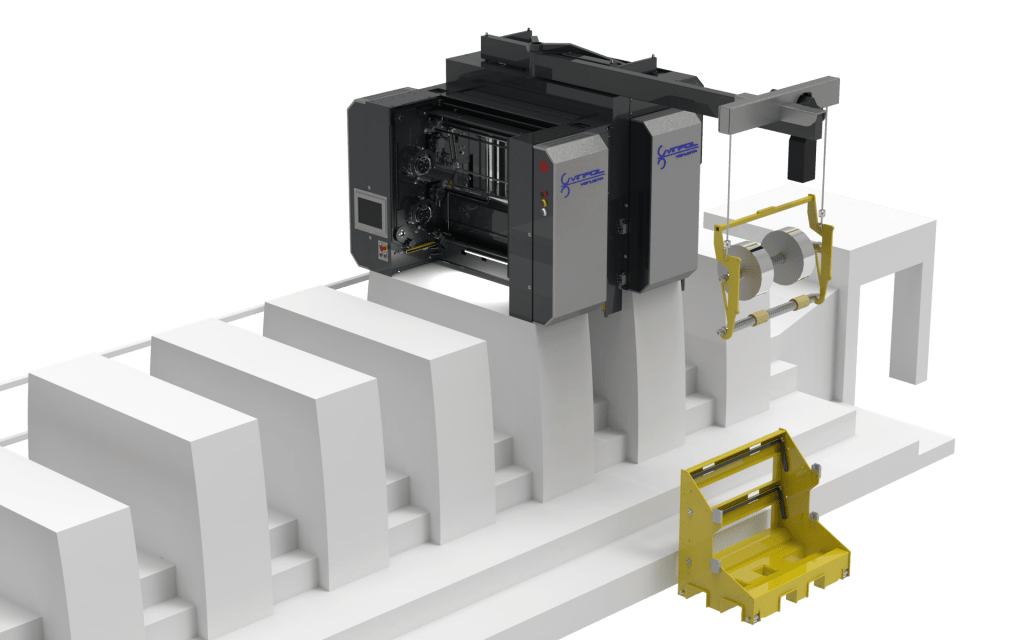
Overhead Reel Manipulator (ORM)
The overhead Reel Manipulator reduces changeover times to a minimum. It is possible to load and unload two locking shafts (unwinding & rewinding) at the same time. Changing the reels takes place at ground level, which ensures a very easy and safe operation. With this option, an external crane is not needed.